This article is published in Inside MRO, part of Aviation Week Intelligence Network (AWIN), and is complimentary through Feb 01, 2024. For information on becoming an AWIN Member to access more content like this, click here.
Opinion: Technician Experience Trumps Paperwork In Parts Scandal
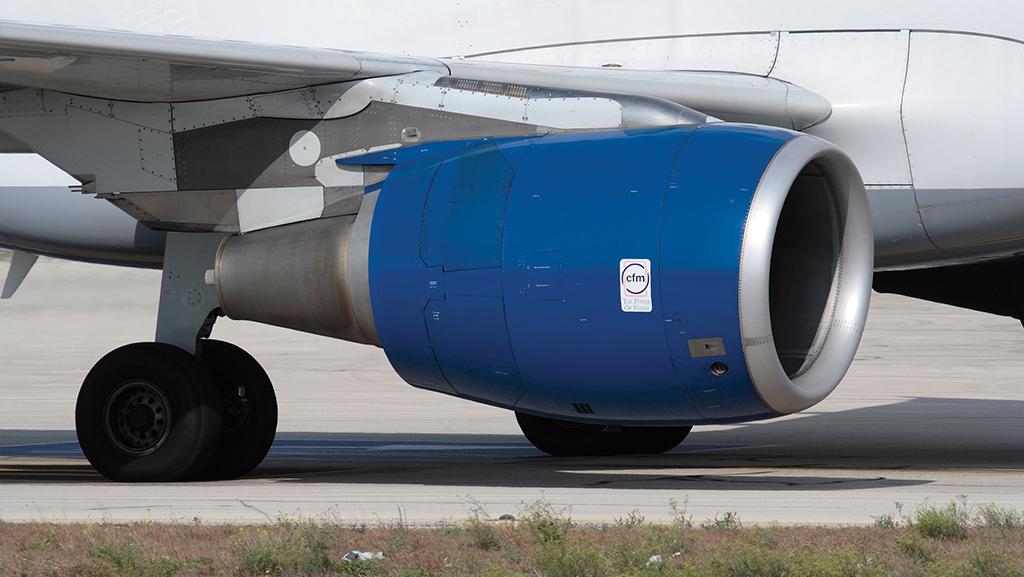
Unapproved CFM56 engine parts from AOG Technics were identified through technician experience, despite falsified paperwork.
In August, the European Union Aviation Safety Agency notified industry that AOG Technics, a UK-headquartered company, distributed “several” CFM56 engine parts with falsified Authorized Release Certificates. The actual number of affected parts is apparently in the thousands. The FAA issued its own unapproved parts notification against AOG Technics on Sept. 21, bringing the issue to the attention of U.S. media and sparking a frenzied review by operators. ARSA answered more than its fair share of “don’t you think”-style leading questions from reporters in the months that followed.
This episode underscores the problem of prioritizing paperwork over technical know-how. Misimpressions about the European Union Aviation Safety Agency (EASA) Form 1’s infallibility have taken hold in industry and in the public mind. Reuters, for example, said that a “release certificate is akin to a birth certificate for an engine part, guaranteeing it is genuine” (emphasis added). It clearly does not. AOG Technics allegedly created counterfeit forms that appeared genuine. Ultimately, it was a mechanic at TAP Air Portugal who identified the problem when comparing the purportedly new part with the fake form.
The allegations against AOG Technics suggest a vast conspiracy to defraud. While the FAA can refer cases to the Justice Department for criminal prosecution, EASA must rely on law enforcement authorities in EU member states. Overreliance on paperwork paired with a lack of clear consequences has left a gap that crooks can exploit. As the Wall Street Journal wrote: “The incident . . . poses questions about the efficacy of the predominantly paper-based system used to track parts and the ease of fabrication.”
In November, industry colleague Brent Webb, CEO of Aircraft Inventory Management and Services, called the situation a “good learning opportunity.” Citing the preamble to the 2003 rule that created 14 CFR § 3.5 (ARSA loves it when preambles are cited), Webb noted that regulations already exist regarding statements about type-certificated products. Reacting to this summer’s drama with more rulemaking would be overreacting.
“The aviation industry identified the issues, not the regulators or the flying public,” Webb explained. “The industry brought attention to itself to do what was right, even though this has eroded some of the trust the public has in the aviation system. The industry is searching hard for not only the parts but also ways to make our industry better, and at the same time, we should be trumpeting that we found the issues and we are making corrections.”
What protected aviation safety against the conspiracy was not a law or regulation but instead the competence of a mechanic smart enough to recognize a used part that was described as “new” on its paperwork. People performing maintenance must have the knowledge gained through training and experience to perform their assigned tasks. Relying on and reinforcing that knowledge is the best safeguard of system safety.
Governments might run on paperwork, but the last line of defense in aviation safety is still what it always has been: a trained and conscientious technician, not a piece of paper.
Christian A. Klein is the managing member of Obadal, Filler, MacLeod & Klein, overseeing the firm’s policy advocacy practice. He represents trade associations as a registered federal lobbyist and provides strategic communications and legal counsel services to clients. He is executive vice president of the Aeronautical Repair Station Association.