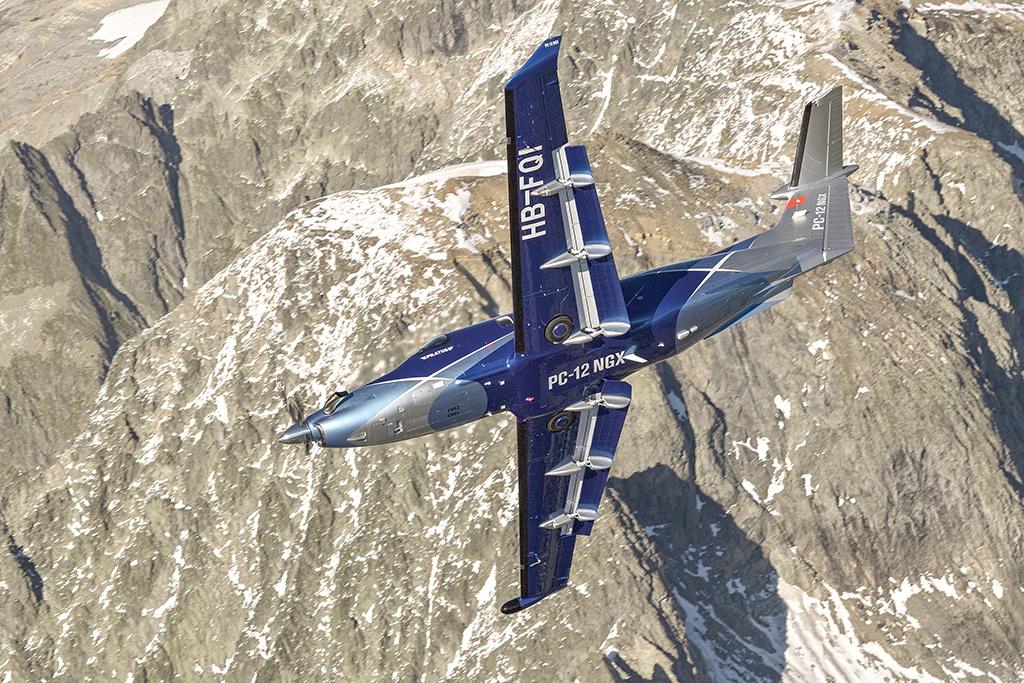
From a distance, it’s tough to distinguish the PC-12 NGX, the fourth-generation of Pilatus’ best-selling single-engine, pressurized turboprop, from those that came before. It bears close resemblance to the original airplane that made its debut more than a quarter century ago.
True to its roots, it still boasts a cabin that has 10% more volume than that of the King Air 250, along with an 18-sq.-ft. aft cargo door and the only flat floor in its class. It’s just as comfortable flying out of a grass strip as it is operating from the nearly 6,000 airports with paved runways. In other words, it remains business aviation’s favorite flying off-road vehicle, offering virtually unmatched utility.
When nearing the aircraft, the NGX’s larger cabin windows, with squarer corners, tip off spotters that it’s the new model. Unbutton the engine cowl, belt into the left seat or nestle into the cabin and dozens of upgrades become apparent.
Up front, there’s Pratt & Whitney Canada’s PT6E with full-authority integrated prop and engine digital controls. P&WC calls it an Engine and Propeller Electronic Control System, EPECS for short. The Canadians call the EPECS a system of systems, as it is linked to fuel and prop controls, stand-alone electronic engine control, and engine trend monitor unit and sensors, among other components. It is mounted low in the engine compartment, well isolated from engine heat and vibration for long life.

From a pilot’s perspective, the only meaningful difference between flying with a PT6E with the EPECS and operating a FADEC-equipped turbofan engine is the five-blade prop spinning on the nose. Look closely under the cowl and you will notice no prop governor and no associated mechanical control linkages. The prop control unit is electronically controlled by the EPECS, hydraulically changing blade pitch with oil pressure.
Similarly, the fuel control unit (FCU) has no mechanical linkages. It schedules fuel flow in response to electronic commands from the EPECS. The FCU has a fuel/oil heat exchanger that warms bypass fuel flow from the engine-driven fuel pump to 50-60C that is then recirculated back to the wing tanks to power the jet pumps. The heated and insulated motive flow system prevents ice from forming in wing tanks and thus eliminates the need for anti-icing fuel additives, such as Prist.
The flight deck has several modifications. Most noticeable is the throttle quadrant. Gone are the manual override and prop condition levers, plus all mechanical linkages to the engine. As with FADEC-equipped turbofans, the PT6E’s power control lever is electronically linked to the EPECS. An optional full-authority autothrottle handles power setting chores from takeoff roll to short final on landing.
The dual-channel EPECS provides fuel scheduling redundancy and the flight/ground idle transition is controlled by a weight-on-wheels switch. The left side of the overhead panel has a simple engine stop/run toggle switch and start button. The EPECS provides start malfunction protection, chock-to-chock torque limiting and prop control, along with automatic dry motoring to cool or purge fuel from the engine as necessary. A prop low-speed mode button reduces prop speed to 1,550 rpm from 1,700 during most phases of flight for considerably lower cabin sound levels. The PT6E has a slightly higher torque limit to assure that all 1,200 shp are available at 1,550 rpm.

The flight deck has been upgraded from Honeywell Primus Apex Build 10 to Build 12. Similar to the PC-24, it is now branded as Pilatus ACE, short for advanced cockpit environment. The displays are much brighter and clearer, VHF VDL Mode 2 CPDLC has been added as an option for Europe, ADS-B In is standard and there’s an emergency descent mode that can be armed above FL 200. Data-link weather services have been upgraded, and the center console now sports a touchscreen control unit that replaces the mechanical keypad and joystick. Overall, the PC-12 NGX’s flight deck is more advanced than the current version of the PC-24’s avionics suite.
The cabin has numerous improvements. Overhead-mounted, drop-down oxygen masks now are optional. The available vapor-cycle air conditioner is more powerful. Most apparent are the new windows that have the same width and height as the older models, but the squarer corners increase area by 10%. At first glance, that seems like a minor change, but it is much easier to look outside because of their different shape. The chairs now fully recline to convert into lie-flat berths. Seat mounts have quick-release fittings that allow chairs to be removed or replaced in minutes.
The headliner has been recontoured to increase seated headroom, improve air distribution and accommodate upwash lighting. Noise levels have been reduced. At 1,550 prop rpm and with the forward lav door closed, the cabin appears to be the quietest in class.
Proven Swiss Structure and Systems
The fourth-generation NGX retains all the ruggedness of the original 1994 model, plus it incorporates the drag-reduction modifications made to the third-generation NG. As with all Pilatus designs, the PC-12’s airframe primarily is fabricated from high-strength aluminum alloys using conventional semi-monocoque construction. The nose cowl is a carbon fiber/nomex honeycomb composite sandwich, covered with a copper mesh for electrical bonding and lightning protection. Composites also are used for various fairings, landing gear doors and wingtips/winglets, plus the dorsal fin extension forward of the vertical stabilizer and ventral fin on the tail cone.

The wings use conventional ladder inner structures, with top and bottom skins riveted to front and rear spars, along with machined and hydro-formed chord-wise ribs. Each wing has an integral wet-wing fuel tank with an over-wing refueling port and a usable capacity of about 1,347 lb.
All PC-12 models feature NASA-derived airfoils developed in the early 1970s. The Swiss chose a modified LS (low-speed) 0417 design for the root that blends to an MS (medium-speed) 0313 section at the tip. The result is a relatively low pitching moment coefficient, good lift-to-drag characteristics in climb and cruise, plus docile stall behavior.
Its predecessor, the NG, has over a half-dozen drag-reduction improvements that, in combination with a Hartzell five-blade, thin-chord, carbon-fiber prop, enable the aircraft to cruise up to 5 kt. faster, take off on slightly shorter runways and climb to cruise altitude 10% quicker. Compared to the first two generations of PC-12s, the NG and NGX have an oil cooler cover that has been reconfigured, a cowl exhaust vent with a flush surface, antennas aligned with the local airflow patterns, gap seals fitted to the flaps, flap track fairings that are more streamlined and a flush-mount operating handle on the main entry door, among other small refinements.
The fuel system has left and right collector sumps, each with a DC-powered boost pump used for engine start, crossfeed and as a backup to the main jet pumps. Fuel balancing is automatic, but it can be pilot controlled in case of a malfunction. Jet pumps also are used to transfer fuel from low points in the tanks to the sumps. The jet pumps use high-pressure bypass fuel from the engine-driven pump for motive flow pressure.

The left and right windshields are glass layers with stretched acrylic sandwiched between the plies. All other windows are stretched acrylic. The main airstair entry door is 2.0 ft. wide by 4.5 ft. tall. There is a 2.1 ft.-high-by-1.5-ft. wide emergency exit plug door over the right wing.
Aluminum is used for all of the primary control surfaces, all of which are manually actuated, with inputs from the control wheel and rudder pedals transmitted to the control surfaces by push-pull rods and cables. There is an aileron/rudder spring interconnect to help prevent adverse yaw or roll, a three-axis electric trim system actuating tabs on the rudder and ailerons, plus a screw jack that moves the trimmable horizontal stabilizer. The ailerons have geared servo tabs that reduce roll control effort by two-thirds, endowing the aircraft with excellent pitch/roll control force harmony. The left aileron servo tab doubles as a trim tab. The elevator has a stall-barrier stick shaker and pusher system to help prevent excessively high angle of attack.
The Fowler flaps are electrically actuated by means of a single motor driving flex shafts connected to gearboxes and jackscrews with 0-, 15-, 30- and 40-deg. preset positions.
The landing gear, having low-pressure tires, is built for rough-field operations. The trailing link main gear have 14 in. of travel. In contrast to the NG, which uses a 28-volt electrically powered, 2,800-psi hydraulic pack to actuate the gear, the NGX uses electric motors and linear motion jackscrews. The gear are held in place by motor brakes. The emergency gear extension system releases the jackscrew actuator gear train so the landing gear can free-fall into position.
Mechanical links through the rudder pedals provide +/- 12 deg. of steering. Differential braking can pivot the nosewheel up to 60 deg.
The 28-volt DC electrical system is a dual-redundant, split-bus design, similar to that of the Eclipse 500 or Embraer Phenom 100. Each side of the split-bus system has its own 42 AH lead-acid battery and 300-amp generator bolted directly to the engine accessory gearbox. The primary side has a pure generator and the secondary side has a combined starter-generator. Standard equipment also includes an emergency power system with a third battery. Optional heated NiCads provide 10% more power than unheated ones. There is a separate, standard 5-amp/hour emergency battery. Notably, the PT6E’s fuel control unit has an integral permanent magnet alternator that powers all EPECS components in the event of a total electrical failure.
The split-bus system is designed for easy operation, with each side carrying designated loads. There are automatic bus tie and automatic load-shedding functions that reduce pilot workload when both generators are not on line. The primary side powers essential equipment and the secondary side supplies non-essential gear. For pre-departure clearance delivery chores prior to engine start, a stand-by bus provides power to radios, the FMS and the MFD map.
The split-bus’s primary side battery powers all avionics and essential equipment prior to and during the initial part of the engine start cycle, thereby protecting it from current surges and eliminating the need to turn off avionics gear before both generators are on line. At 10% rpm, the primary side battery automatically ties into the secondary side to assist in cranking the engine. The delay function improves cranking performance to prevent hot starts as well as current surges. With both generators on line after start, the electrical system reverts to the normal split-bus configuration.
Both generators must be on line to power the standard auxiliary electric heaters or optional vapor-cycle system (VCS) air conditioner. The refrigeration system has been upgraded with separate motors for the compressor and condenser cooling fan, thereby eliminating the belt drive in older versions. Air distribution is improved to increase flow and reduce noise.
If external power is available, it can be used to power equipment on all buses, including the electric heaters or VCS air conditioner. External power also is the only way to provide power to all four Primus Apex screens prior to engine start because of the system’s automatic load-shedding design.
Ice protection is provided by deice boots on the wing and horizontal stabilizer leading edges, exhaust heat ducted through the engine inlet lips and a particle separator that can be deployed in the engine air intake duct. Electric heaters provide anti-ice protection for the windshields, probes and static ports.
Pressurization is modulated automatically by a dual-channel, electronically controlled system that uses FMS-derived landing field elevation. If the destination airport is not in the FMS database, the crew can program in landing field elevation. That’s a useful function if your destination is an uncharted grass strip next to your favorite fishing lodge.
A standard pneumatically controlled safety outflow valve backs up the automatic system to prevent over-pressurization. Cabin altitude is 8,000 ft. at FL 262 and 10,000 ft. at FL 300, the aircraft’s maximum certified operating altitude.
The NGX has a dual-zone temperature control, albeit one limited to providing a +/-9F (5C) difference between the cockpit and cabin. Temperature sensors in the cockpit and cabin provide actual temperature indications on the ACE flightdeck displays.
The airplane has ample heating capacity, as dual under-floor electrical aux heaters are standard equipment. Additional electric foot warmers for the pilots are optional. The standard aircraft has an air-cycle machine (ACM) that provides air conditioning once the engine is running. But the bleed air supplied to the ACM by the engine is too meager to provide much cooling in warm climates. Serial number 2001, the aircraft we flew for this report, has the optional VCS air conditioner with the higher volume air distribution system. We recommend ordering that option.
Standard kit includes three 10.4-in. ACE displays — pilot’s side PFD, plus stacked MFDs in the center panel, along with a solid-state standby instrument display that eliminates the need for a “wet” compass. The base model is fitted with a single SBAS GPS receiver, single ADS-B capable Mode S transponder, dual comm and nav radios, single radio altimeter, DME transceiver, ADF receiver and RDR 2000 4-kW magnetron weather radar with vertical scan mode. Also standard are a 406 MHz ELT with GPS position input, data recorder, TCAS I, Class B TAWS, PFD synthetic vision, coupled VNAV with FMS 3-D visual approach guidance, and RVSM capability, along with pilot-defined FMS approach guidance, vertical glidepath, vertical situation display on the MFD and coupled VNAV.
A tactile feedback function, using the autopilot aileron servo, has been added to help nudge the aircraft back to a 31-deg. bank angle, should the pilot inadvertently exceed a 51-deg. bank angle when hand-flying the aircraft. Tactile feedback may be overridden by pressing the touch-control steering button, thereby releasing the aileron servo clutch.
A fourth, copilot-side 10.4-in. PFD is optional, along with available Sirius XM satellite data-link weather, 6-kW weather radar, second SBAS GPS receiver, ATN B1 CPDLC for Europe that piggybacks on VHF comm 2, second Mode S ADS-B capable transponder, and dual iPad Mini mounts. Other options include TCAS II, 2-D airport maps with ADS-B In cockpit display of traffic, autothrottle, Aerowave 100 Inmarsat or Iridium satcom, electronic checklist (not interactive), USB charging ports on the flight deck, electronic charts, Honeywell SmartRunway and SmartLanding hazard alerting systems, Bluetooth connectivity between tablet devices and FMS, and Stormscope lightning detector, among other equipment. Honeywell’s Go Direct Flight Bag Pro, running on iPads, can be used to upload flight plans to the FMS, but ACE is not yet interactive with ForeFlight.
Let’s Go Flying
Serial number 2001, ordered by Pilatus Business Aircraft of Broomfield, Colorado, as a demonstrator, is loaded with options. The baseline aircraft weighs 6,373 lb. with a single 200-lb. pilot. Upgrades include the Global Choice USA option package, including virtually all of the avionics options already listed, plus TCAS/ADS-B In vertical separation approach guidance, airport moving map with ADS-B In for both aircraft and surface vehicles, advanced satellite graphical weather, plus a second FMS, steep approach capability, pulsing landing lights, Class A TAWS, heated dual NiCads, USB-A and -C charging ports on the flight deck, and cockpit foot warmers, among other items that add $870,703 to the base price.
The cabin is outfitted with the $455,000 Executive 6 + 2 interior, including six individual chairs that track fore, aft and sideways, swivel and fully recline, plus two removable, occasional-use seats for the aft cabin, along with airstair lights, USB charging ports, five AC power outlets and various other niceties. As befitting a $5.75 million business aircraft, customers are afforded a wide selection of leathers, fabrics, cabinet finishes, metal plating and interior designs. A special NGX paint scheme adds $30,000 to the demonstrator. Total retail price is $5,745,703. Options boosted the BOW by 496 lb., to 6,869 lb., giving it a 922-lb. payload with full fuel.
Demonstration pilot Brian Mead belted into the right seat and I took the left. With Tom Aniello, Pilatus Business Aircraft vice president of marketing, in the cabin, 30 lb. of cargo and 2,035 lb. of fuel, ramp weight was 9,345 lb.
Computed takeoff weight was 9,300 lb. Rocky Mountain Metropolitan Airport’s (KBJC) field elevation is 5,673 ft. Using the PC-12 Pilatus performance iPad app, we plugged in pressure altitude, altimeter 30.11, 25C OAT, a flaps 15-deg. takeoff configuration and normal 1,700 prop rpm. Takeoff distance (TOD) on 7,002-ft.-long Runway 30L was 3,908 ft. and accelerate/stop (A/S) distance was 3,774 ft. Rotation speed was 78 KIAS, flap retraction speed was 100 KIAS, Vx (best angle), Vy (best rate) and Vt (en route climb) speeds were 120 KIAS, 130 KIAS and 140 KIAS, respectively. We could have shaved 400+ ft. off those distances had we used 30-deg. flaps to enhance short-field performance. We opted to use flaps 15 deg. to improve power-off gliding performance in the event of engine failure.
Alternatively, we could have selected 1,550-fpm prop low-speed mode and flaps 15 deg. for noise abatement. TOD and A/S distance would have been 4,536 ft. and 4,231 ft., respectively.
Prestart cockpit checks are short and straightforward. However, there are a half-dozen or so switches and indicators on the left armrest, left and aft of the pilot’s chair, that are difficult to see, let alone check by feel. It’s best to check those with a flashlight before strapping into the seat.
Once the battery switches on the overhead panel are turned on, the FMS may be programmed via the Flight Management Window pages on the MFD, using point, type and click conventions similar to Dassault’s EASy layout. FMW control bar tasks are divided into three phases of flight tabs: pre-takeoff, departure and arrival. The touchscreen control unit may be configured with either an alphanumeric or conventional qwerty virtual keyboard.
Entering the data by hand into ACE sparked three thoughts. First, there’s no iPad-to-ACE FMS connectivity for automatically sharing computed flight plan data. You cannot yet conduct preflight planning tasks on the ground and push the data to the airplane once it is powered up. The tablet-to-airplane interface is on the list of Honeywell and Pilatus IOUs. Second, the NGX’s ACE lacks a tabular performance computer to calculate TOLD (takeoff and landing distance) data, so it has to be entered manually, increasing the risk of fat-finger errors. Third, ACE’s EFIS color conventions are inconsistent.
In our opinion, it would be easier to master the system if cyan were used for all pilot-entered data and magenta for all computer-generated targets. Ideally, green would indicate active (and ILS navigation) status and white would signify standby status.
Pre-start checks aboard the NGX are virtually unchanged from the NG, including the recommendation to open the engine intake inertia separator door to prevent FOD. Serial number 2001 has the optional electronic checklist. But it’s not linked to aircraft systems or switch positions, so each item must be checked off manually as it’s completed.

Starting the PT6E, though, is quite different than starting the PT6A. Flip the engine switch from stop to run and press the start button on the overhead panel, and the EPECS automates all start tasks. Fuel boost pumps come on line, the starter engages, ignition and fuel flow begin, the prop unfeathers, both generators come to life, the engine stabilizes at idle, and fuel boost pumps are turned off when motive flow pressure is sensed.
Weight-on-wheels switches signal the EPECS to set a 64.5% gas generator ground idle speed. After brief ice protection and stick pusher tests, we were ready to taxi from Pilatus Business Aircraft’s ramp to the runway. Our flight plan called for flying the PLAIN1 departure with the AKO (Akron, Colorado) transition, then proceeding to KLBF (North Platte, Nebraska) for a full-stop landing. We filed for FL 270, but we would later ask for FL 290 for a cruise performance check.
Once cleared for takeoff on Runway 30L, we armed the autothrottle and pushed up the power control lever about two-thirds travel. The autothrottle engaged and smoothly advanced the lever to 44.3-psi torque, producing 1,200 shp at 1,700 prop rpm. With 1,550-rpm prop low-speed mode selected, the EPECS would have boosted torque to 44.84 psi to achieve rated takeoff power.
The system enabled us to concentrate our scan outside the aircraft, hawking heading control and watching for runway intrusions. There was no need to babysit the engine as would have been required when flying with the PT6A.
We rotated at 78 KIAS, accelerated through 100 KIAS, retracted the flaps, closed the inertia separator door to boost intake efficiency and selected flight level change on the glareshield mode control panel. The autothrottle automatically adjusted power to the maximum climb setting.
Denver Departure Control assigned us multiple headings and intermediate altitudes to route us around the north side of Denver International, keeping us clear of traffic conflicts. The ADS-B In function enabled us to identify the registration number of each of the potential intruders, as well as see their altitudes, tracks and ground speeds. At each intermediate level-off, the autothrottle adjusted power to maintain either FMS preset speed or the airspeed we dialed into the flight guidance panel.
Handed off to Denver Center, we continued our climb to the northeast toward Akron. Passing through FL 180, it became apparent that the PT6E-67XP offers improved climb performance up to the aircraft’s FL 300 maximum cruise altitude. The engine is rated at 1,825 thermodynamic hp for climb versus 1,745 thp for the PT6A-67P in the NG. If 1,550-rpm prop low-speed mode is used instead of the normal 1,700 rpm, it adds about 10% to climb time, climb fuel and climb distance.

We turned on the autopilot and let the aircraft stabilize at 24.9-psi Tq (torque) max cruise power set by the autothrottle at FL 290. At a weight of 9,000 lb. in ISA+15C conditions, the aircraft attained a 262-KTAS cruise speed while burning 344 lb./hr., 2 kt. slower and 6 lb./hr. less than book predictions. Notably, it’s up to the crew to keep the engine within recommended temperature limits during cruise as that function is not programmed into the EPECS.
Book cruise numbers for the PC-12 NG, in contrast, predicted 258 KTAS while burning 336 lb./hr. If you expect the aircraft to cruise at its advertised 290 KTAS max speed, you’ll have to unload most of the interior, empty the fuel tanks to 100 gal. and fly it between 19,500 and 24,500 ft. while burning close to 500 lb./hr. Everyday cruise speeds, in contrast, are 280 to 285 KTAS in the high 20s while consuming 380 to 420 lb./hr., assuming standard day temperatures.
Then we selected prop low-speed mode, reducing rpm to 1,550 and increasing Tq to 27.2 psi. Speed increased to 265 KTAS, 2 kt. faster than book, and fuel flow steadied at 345 lb./hr., or 7 lb./hr. less than book predictions.
Our cruise performance measurements were anecdotal, at best, because of unstable atmospheric conditions and building cumulus nearby. Using book numbers rather than inflight observations, we concluded that reducing cruise rpm from 1,700 to 1,550 costs only 1-2 kt. and increases fuel flow by about 2%, while slashing interior sound levels by several dB. Passengers are going to notice the reduction in sound levels at 1,550 prop rpm.
We then proceeded direct to North Platte Regional Airport Lee Bird Field and programmed the FMS for a right-pattern, downwind visual entry to Runway 12. Left-, right- and straight-in VFR pattern guidance are new features added to the NGX’s ACE system. We used the flight guidance track mode to set a course directly to the downwind entry point and engaged VNAV with a 3-deg. descent path to arrive at pattern altitude a few miles outside of the airport.
Activating left- or right-pattern visual approach guidance causes the FMS to create three temporary waypoints: (1) abeam, offset 1 mi. from the runway threshold, (2) base, 2 mi. downwind from abeam, and (3) final, aligned with the runway centerline and 2 mi. from the threshold. The preset lateral distances can be changed, if required, by the crew.

There is full vertical guidance during visual approach, including a preset synthetic 3-deg. glidepath on final. The preset glidepath angle can be changed by the pilot if it is necessary to clear obstacles, such as trees or power lines, on final approach.
The FMS commands autothrottle speeds of 150 KIAS at flaps 0 deg., 110 KIAS at flaps 15 deg., 100 KIAS at flaps 30 deg. and 90 KIAS at flaps 40 deg. We used flaps 30 deg.; turning final we manually selected 85 KIAS for Vref. Book landing distance was 2,600 ft. for the 8,600-lb. aircraft.
If the autopilot had been coupled, it would have provided 3-D guidance from FL 290 all the way down to short final on the visual approach. But the aircraft is so enjoyable to hand-fly, we didn’t defer to the computers.
It’s almost impossible to make a hard landing in the PC-12 because of its exceptionally long travel, trailing-link main landing gear. But it is possible to float for several hundred feet if you’re carrying excessive speed in the flare.
Memo to self: Disconnect the autothrottle over the threshold and pull back the power lever to idle. The aircraft has plenty of energy to decelerate slowly, especially as flight idle prop pitch produces very little drag at low indicated airspeeds.
After a breakfast break at North Platte, we departed the airport, engaged the autopilot and programmed the FMS to guide us to Akron’s Colorado Plains Regional Airport (KAKO). We plugged in the RNAV GPS Runway 29 approach and let the autopilot and autothrottle handle the rest. At decision altitude, we pressed the go-around button on the throttle and observed the coupled go-around capability of the flight guidance system. Outside of landing gear and flap configuration changes, ACE handles the rest. The combination of a full-function flight guidance system and autothrottle greatly reduces pilot workload.
After a few touch-and-goes in the pattern at Akron, we proceeded VFR back to Broomfield to land on Runway 12R. En route, we noted that the flight deck on this particular aircraft doesn’t appear to have much flow from the air-conditioning gaspers, so it gets uncomfortably warm at low altitude in direct sunlight.
Conclusions, Competition, Cost
The NGX climbs quicker, cruises faster and is far more capable than any previous version of the PC-12. It’s more comfortable, quieter inside and considerably easier to fly because of its upgraded FMS, computer-controlled engine and prop, and autothrottle. But gaining FMS proficiency takes practice on the ground to avoid getting your head buried in the cockpit during flight.
The cabin of the aircraft has the feel, quiet and comfort of a light jet. The new windows make it appear wider than its measurements indicate, the upgraded seats are more accommodating and the interior is impressively quiet in cruise at 1,550 rpm, especially with the forward door to the lav closed.
The NGX is also less expensive to operate than previous PC-12 iterations because of its extended maintenance intervals and increased TBO. It simply spends more time in the air and less time in the shop.
Glance, at this year’s BCA Purchase Planning Handbook in the June/July issue. There are seven high-performance, pressurized single-engine turboprops. The Epic 1000, the newest entrant, is the most affordable, it is the highest flying and has virtually unmatched cruise speed. The Piper M600, while being in the Epic 1000’s price range, cruises lower, slower, with less tanks-full payload and the tightest cabin dimensions in class. Daher’s TBM 900-series aircraft are comfortable, efficient and long range, as well as having up to a 40-kt. speed advantage over the PC-12 NGX. Notably, all other single-engine turboprop competitors have Garmin avionics packages that offer, or soon will offer, an emergency auto-land capability. That’s a significant advantage for single-pilot operators, a feature that Honeywell and Pilatus have yet to develop.
On balance, however, none of those competitors has the complete feature set of the PC-12 NGX. They lack its rough-field capability, its large cargo door, its roomy 6-8-seat cabin and its full cabin width, albeit forward, lavatory. The NGX is the only business aviation turboprop in current production to have a computer-controlled engine and prop system. Its PT6E engine has nearly 40% longer overhaul intervals and lower hourly maintenance costs than competitors powered by the PT6A.
As shown in the accompanying specifications table, the PC-12 is the largest, heaviest and most-expensive model in the single-engine turboprop class. It continues to sell strongly with roughly double the deliveries of its closest competitor, even though typically equipped it’s $1 million more expensive. The fourth-generation NGX increases the value of the PC-12, keeping it in a class of its own.