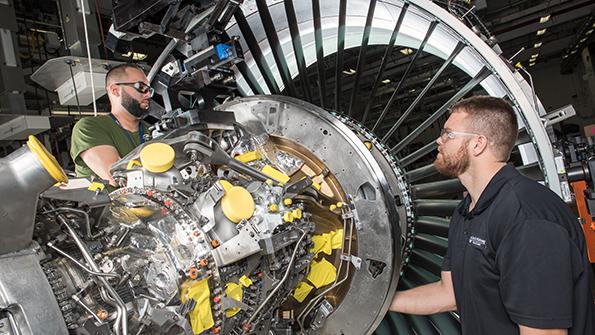
Airbus CEO Guillaume Faury referred to 2022 as a “lost year” on the OEM’s 2022 earnings call: The 661 full-year deliveries were 60 aircraft light of the company’s targets at the start of the year and below even the 688 deliveries Airbus achieved as long ago as 2016.
It has seemed increasingly quixotic lately for Airbus to talk boldly about its plans for a production “ramp-up.” The company’s medium-term targets (for 75 A320-family aircraft , 14 A220s and up to 10 widebodies monthly) would lead to deliveries in the second half of the decade exceeding 1,000 a year. But recent monthly output has flatlined, showing almost no visible signs of a pickup from the low point of 2021.
Any OEM will acknowledge, if only in private, a supplier that appears at the top of its “risk register,” held to blame for many production or quality shortfalls. For Airbus, until recently, CFM and Pratt & Whitney, responsible for powering both the A320 and A220 programs, were top of the list. But dig only slightly deeper, and the industry’s overdependence on a perilously narrow base of producers of forgings and castings becomes apparent. It should be no surprise that Airbus and Safran have together bailed out and acquired French alloys and forgings producer Aubert & Duval—the last thing the two OEMs needed was a further reduction of supply options. And there is no room in civil aerospace at the moment for false conceptions about the merits (or otherwise) of vertical integration.
But CFM and Pratt & Whitney are not in the clear yet. Even as their production systems spool up, availability problems with their workhorse Leap and PW1100G engines are cropping up, both in airline operations and in their own bottom lines. Pratt & Whitney appears to have the most immediate problem, with widespread reported groundings of Airbus A220 aircraft and near-systemic problems for Indian airlines—Go First, a low-cost carrier, has even publicly blamed unreliability of the PW1100G for its own bankruptcy. But CFM has problems, too, with Leap engines that are operated in sandy environments experiencing times between overhauls far lower than expected. This in turn pushes back the profitability of both spare engines and long-term service agreements.
Ultimately, even the engine manufacturers cannot defy the laws of physics: CFM and Pratt & Whitney both went from mature legacy narrowbody designs (the CFM56 and V2500, respectively) and achieved step changes in efficiencies. But running the new designs hotter (Leap) and/or leaner (PW1100G) has given rise to the very same problems that plague widebody engines, most notably Rolls-Royce’s Trent 1000. The process of designing and fitting the necessary upgrades likely will take years, and in the nearer term, the engine-makers have to juggle the availability of finite quantities of spare parts for maintenance, repair and overhaul shops and whole engines between the airframers and airlines with grounded aircraft.
The civil aerospace industry is suffering from an institutional form of “long COVID.” The decisions and actions taken (in most cases entirely appropriately) in the dark quarters of 2020-21 are proving far harder to reverse—and even longer to recover from—than company leaders might have expected, given experiences with previous down-cycles. Leaders on a number of earnings calls have noted that many of their most experienced personnel left as the industry turned down in 2020, and the employees who remain, plus the most recent joiners, are on average materially less qualified and frequently far less flexible. This is a poor employment foundation on which to build a near doubling of production.
This loss of skills is having an impact on both sides of the Atlantic. Airbus changed A320 program management and reinstated its “watchtower” process to identify and work with poorly performing suppliers. And the bar for Boeing’s production rate ramp is pretty low: About one-third of 737 MAXs being delivered are coming out of previously built stock, although Boeing and key partner Spirit AeroSystems have at times given the impression that they have all but forgotten to build the 737 MAX to a consistent (acceptable) level of quality.
Supply chain problems increasingly may resemble “whack-a-mole” for the OEMs as they chase shortages of forgings, semiconductors, cabin furnishings and seats through supply chain tiers.
It is too early to write off 2023 as another “lost year” in the commercial aircraft recovery from the COVID-19 pandemic. But investors are taking OEM production targets and the resultant near-term financial guidance with progressively larger pinches of salt.
The views expressed are not necessarily those of Aviation Week.