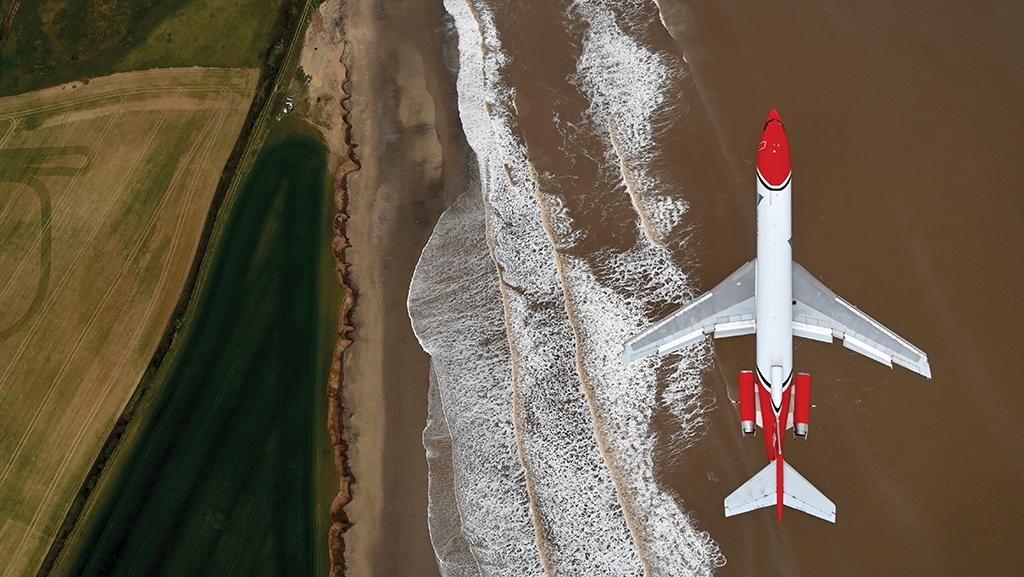
The 727 crews must be ready to tackle oil spills at sea and even near land, where the oil could be devastating for seabirds and animals.
It is a rather strange sensation, flying low at 150 ft. over the North Sea. Foaming waves and seabirds speed by, but this is not a high-performance combat aircraft or a submarine-hunting maritime patroller—it is a 1970s-era Boeing 727 freighter that once shuttled packages between U.S. cities for FedEx. Since 2016, it has been on standby year-round as one of two 727s equipped for oil spill dispersant delivery and one of the few 727s still flying commercially.
The first jet-powered aircraft used against oil spills, they have since been joined by an adapted Boeing 737-400 freighter flown by competitor RVL Aviation on behalf of the UK Maritime and Coastguard Agency.
- The Tersus system can hold 4,000 gal. of oil dispersant
- The aircraft is on standby for worldwide operations
Operating the 727s is UK-based aerospace engineering company 2Excel Aviation on behalf of Oil Spill Response, an oil industry joint venture established to deal with and clean up oil spills before they cause serious environmental damage. The 727 is a first responder—the aircraft and its crews can be called out at a few hours’ notice to anywhere in the world.
This level of alert continues despite recent upheavals that forced 2Excel to leave its Doncaster Sheffield Airport home when owner Peel Airports decided to close the facility last November, forcing the 727s to relocate quickly to Teesside International Airport near Middlesbrough, England.
Such missions previously relied on types such as the commercial-variant Lockheed L-382 Hercules and hastily converted piston engine airliners. But the slow speed of those earlier aircraft meant it could take days to deploy them to remote regions where they might be needed. The 727 can fly anywhere in the world in less than 24 hr. Although the aircraft has yet to be called out on its stated mission for 2Excel, it did deploy to Djibouti in July amid concerns about a floating storage and offloading unit off the Yemeni coast.
The 727 is equipped with a specially developed system called Tersus—Latin for “clean”—on its main deck and can carry up to 15,000 liters (4,000 gal.) of dispersant liquid. Delivered from a spray bar underneath the rear-mounted engines, the dispersant chemicals bind with oil floating on the surface of the water, helping drag the oil to the bottom of the sea and breaking it up before it can damage beaches and kill wildlife such as seabirds. The Tersus system is compatible with a number of dispersants developed to tackle the large variety of oils extracted worldwide and their varying chemistries.
About 2,000 ft. above, a Piper Navajo spotter aircraft guides the 727’s crew down toward the simulated oil spill. Once in position, the aircraft attacks the spill with a series of low flybys over the water, spraying the dispersant before climbing away to repeat the maneuver. In its next passes, it sidesteps the previous dispersant drop like one mows a lawn, as described by Arnie Palmer, 2Excel’s director of special missions, flying in the right-hand seat during a training flight in April. “There is an art to this,” he said. “We need to fly as low and slow as possible.”
If the aircraft flies too fast, the dispersant becomes more of a mist and cannot deliver its intended effect. Spraying is generally done at a steady 150 ft. and 150 kt., with a slight nose-up attitude. Turning on the spray system inhibits the ground-proximity-warning systems, and the air conditioning is turned off to reduce the load on the engines in the event of a single- or even double-engine failure.
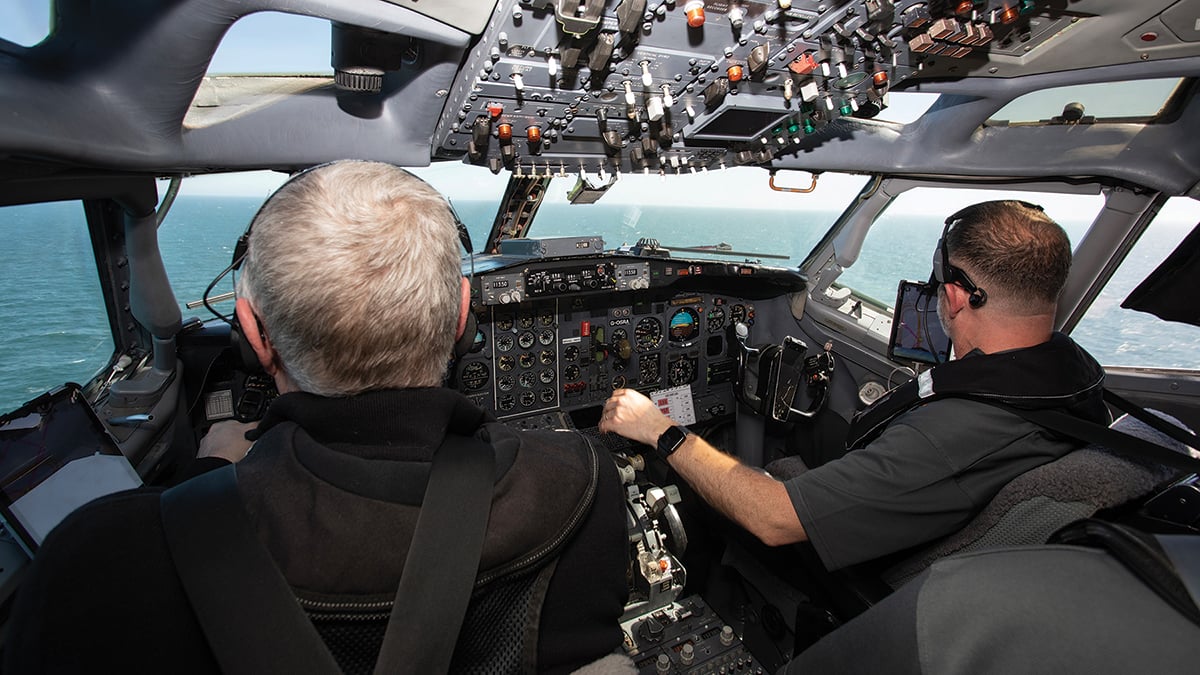
The Tersus system’s pumps are prearmed and recirculate the fluid so that the system can begin spraying without delay. During each 45-60-sec. low pass, the cockpit atmosphere is calm. The 2Excel crews regularly fly training dispersant delivery training sorties, so operating the big jet at a low altitude is now routine. Ian Cameron, 2Excel’s head of counterpollution, is on the flight controls, while Palmer monitors the thrust levers and flight engineer Steve Armson, one of the handful of commercial 727 flight engineers left in Europe, looks after the spray system and reads out the altitude, the pitch of his voice increasing as the altitude decreases.
On the day we flew, conditions were almost perfect: The sea was calm, visibility unlimited and the Tersus system delivered water instead of dispersant—about 1,000-1,200 liters during each of our six passes. The real kerosene-based dispersant is not used for training and can be harmful to wildlife itself if sprayed onto the water’s surface without an oil slick present.
“The 727 is ideal for this mission,” Cameron says. “If we lose an engine, there’s not much asymmetric [thrust] and we can climb away on one [engine] if we need to.”
The aircraft, registered as G-OSRA and G-OSRB, are among the last 727s built and received the Valsan engine upgrade, which equipped them with a pair of Pratt & Whitney JT8D-217s in the engine pods. The -217 is the engine used in the McDonnell Douglas MD-82. A JT8D-9-15 engine remains at the very rear. In the event of an engine loss at low altitude, the crew would firewall the engines and put as much distance between the aircraft and the water as possible. The aircraft’s performance is crucial—oil spills may not always occur in open water but closer to the land with obstructions such as cliffs, wind farms, oil rigs and shipping to consider.
The unlikely new role for the 727 was prompted by the Deepwater Horizon accident in the Gulf of Mexico in July 2010, after which oil companies realized they needed to respond to such incidents more rapidly.
Development of the complete Tersus system was led by 2Excel Aviation at its Lasham, England, facility, where the roll-on, roll-off system of tanks and pumps was initially developed. The company prides itself on delivering on challenging aerospace engineering projects. But in 2014, just as the program was in its final stages and close to delivery, regulators declared the dispersant was a flammable liquid and should be treated as such. This required a complete redesign of the system to bring it more closely in line with that associated with an aerial refueling aircraft. The rules called for the spray systems and dispersant storage systems to be double-skinned, able to survive accidents with forces up to 9g without spilling and capable of being vented or drained through systems separate from those already on the aircraft.
The experience of developing Tersus, 2Excel hopes, may put the company in a good position for Oil Spill Response’s future airborne dispersant requirements—the current contract expires at the end of 2028. 2Excel is working on its proposal, which is expected to make use of the 727’s successor, the 757. The company is familiar with the 757 through its work on the Excalibur flight-test aircraft to support sensor and system development for the Tempest combat aircraft for the three-nation Global Combat Air Program.